Paper Cutlery Machine
The NS-PCTM Paper Cutlery Machine segregates its functions in three parts; first, Glue layer coating & Lamination & Die cutting part; second, Forming part and last, Glue Sealing & Drying part. With the increasing awareness of health hazards caused from using plastic cutleries lately, Paper Cutlery Machine came into more popularity with its varied utility- Paper Knife Fork And Spoons.
NS-PCTM
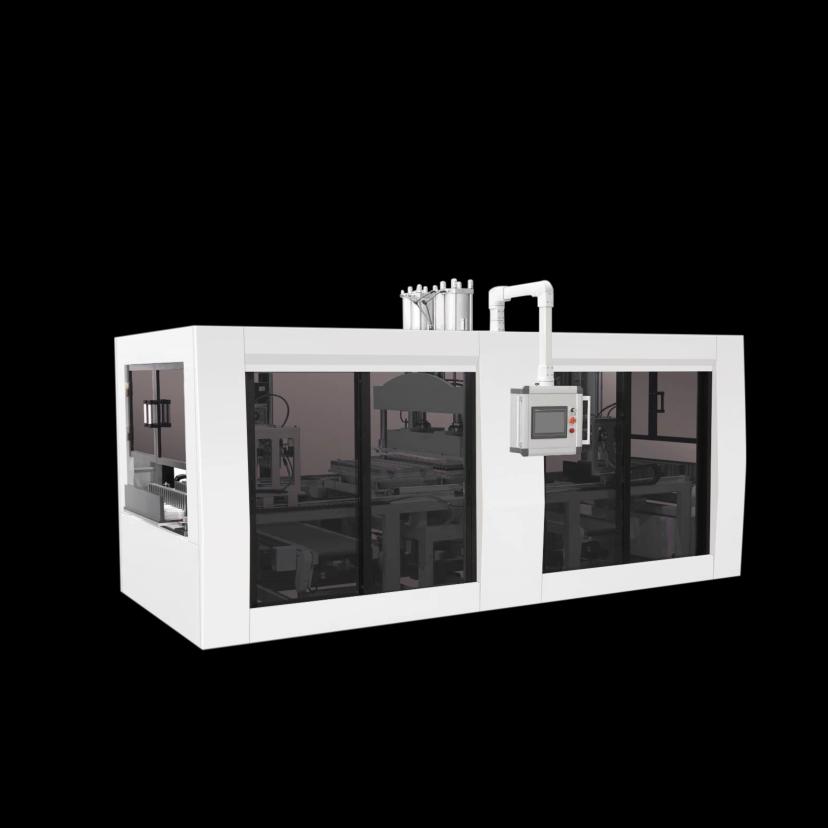
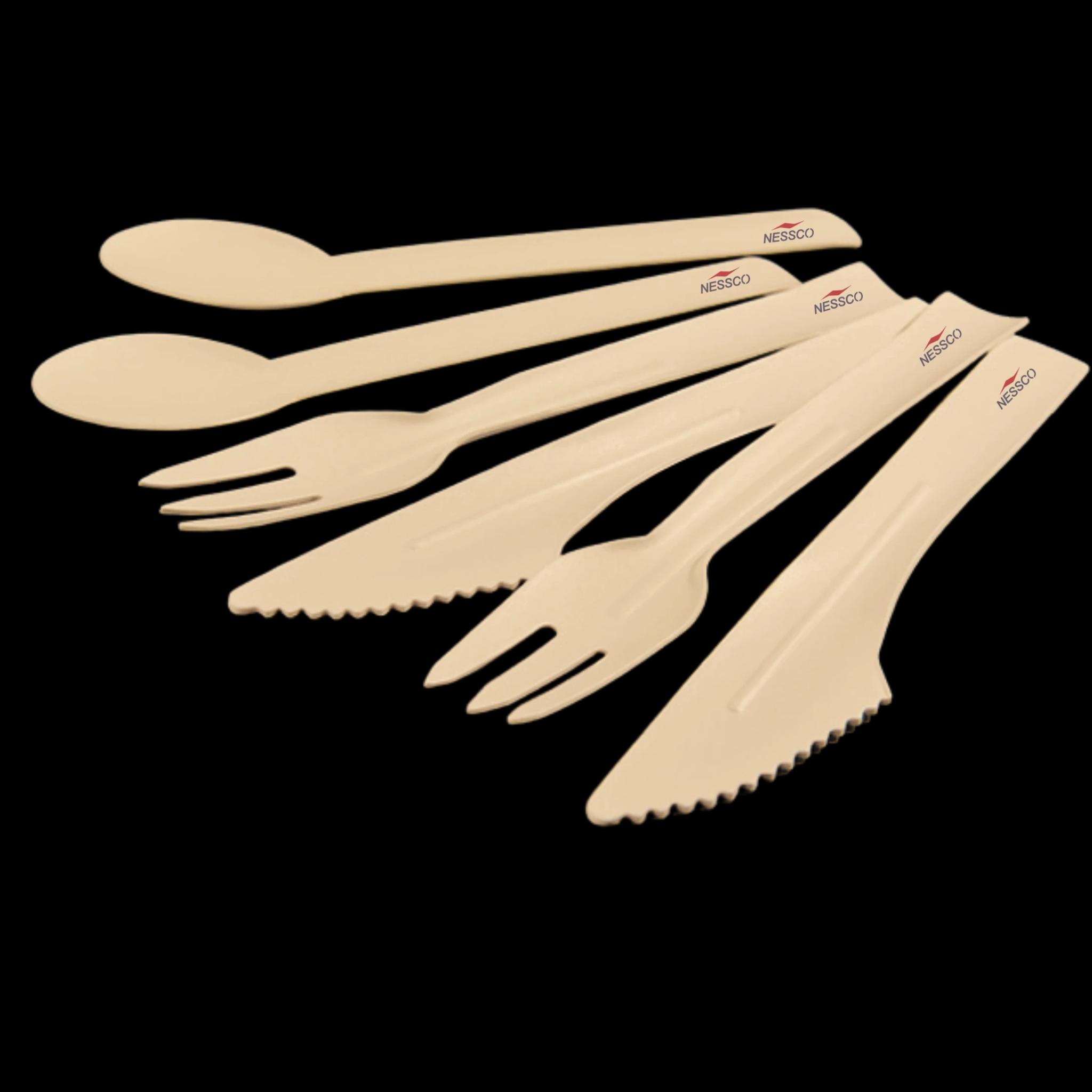
Speed
170 Pcs/Min.
Paper Specification
60-150 Gsm
Size Range
N/A
A paper cutlery making machine is an automated piece of equipment designed to produce disposable cutlery items such as forks, spoons, and knives made from biodegradable paper or paper-based materials. This machine takes rolls of paper or paper pulp and processes them through a series of stages that include shaping, molding, and pressing to create the desired cutlery shapes. The machine often incorporates features like heat sealing and coating applications to enhance durability, water resistance, and usability. This type of machinery supports sustainable manufacturing practices by producing eco-friendly, single-use cutlery that serves as an alternative to plastic, aligning with growing environmental concerns and regulations.
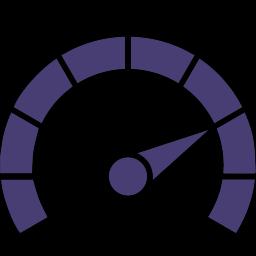
Speed
170 Pcs/Min.
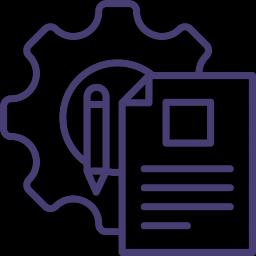
Paper Specification
60-150 Gsm
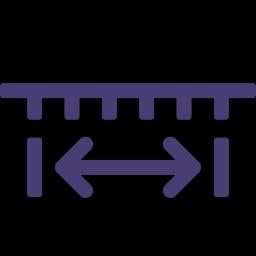
Size Range
N/A
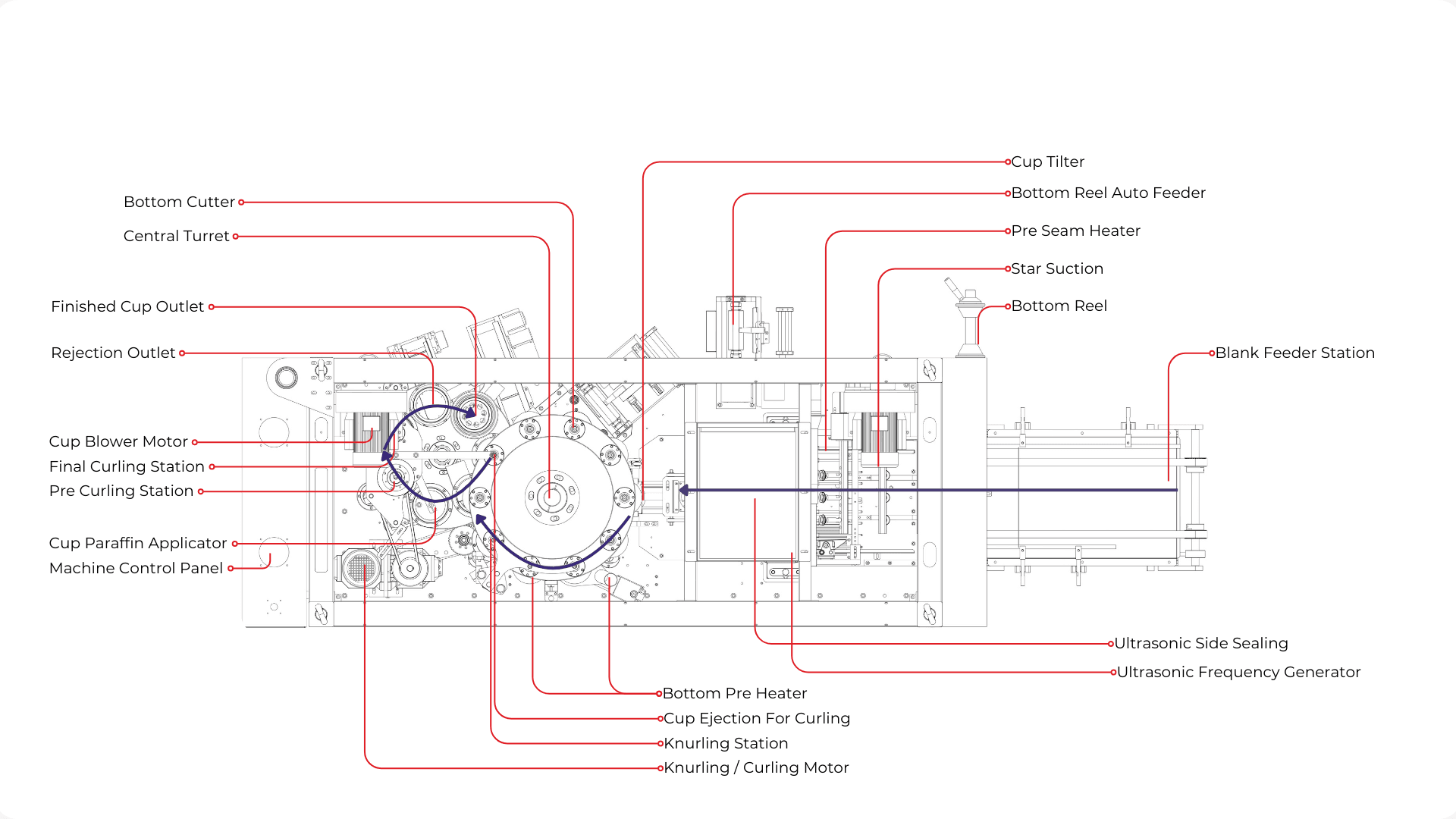
Process of Paper Cutlery

1. Paper Roll
The process begins with the sourcing of large paper rolls, typically made from food-grade paper that has been coated with a thin layer of polyethylene to make it waterproof. These rolls are the raw material that will be transformed into paper cups.

2. Printing
In the printing stage, the paper is fed into a high-speed printing machine that applies custom designs, logos, and other branding elements to the paper. This step is essential for creating branded cups that can be used for promotional purposes in cafes, restaurants, and events.

3. Cutting
After printing, the paper rolls are sent to the cutting machine, where they are precisely cut into flat, fan-shaped pieces known as blanks. These blanks will form the body of the paper cup. Accurate cutting is critical to ensure that the pieces fit together perfectly during the forming stage, avoiding any gaps or misalignment.

4. Paper Fan
The cut blanks are then shaped into a fan-like structure, ready to be formed into the cylindrical body of the cup. This step is important as it begins to give the paper its cup-like shape. The fan-shaped blanks are designed to make it easier to form a tight seam when the edges are joined together.

5. Forming
In this stage, the paper fan is rolled into a cylindrical shape, and the edges are sealed together to form the body of the cup. The machine uses heat and pressure to bond the edges of the paper and create a strong seam. This step transforms the flat blanks into the final cup shape, which is then ready for the next stage.

6. Final Paper Cup Product
Once the cup body is formed, the bottom of the cup is sealed using a separate machine. This step involves applying a bottom piece and sealing it with heat and pressure to ensure the cup is watertight. This final step ensures that the cup can hold liquids without leaking.
Applications
Technical Specifications
FEATURE | SPECIFICATION |
---|---|
Speed | 170 Pcs/Min. |
Paper Specifications | 600-1000 Gsm |
Raw Materials | Environmental Paper Rolls |
Voltage | 380V,50Hz |
General Power | 65 Kw |
Weight | 9070 Kg |
Dimensions | 16000X7000X3000 (mm) |
Air Flow Rate | 30 Cfm |
Air Presssure Rate | 6-8 Bar |
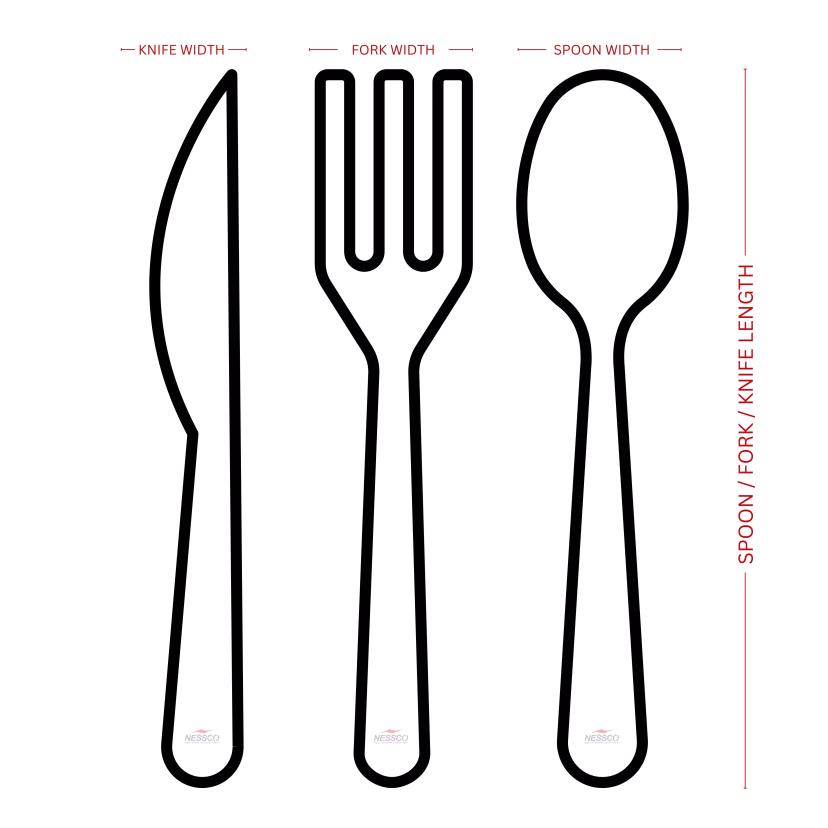
Want to Know More? Enquire Now
Download Brochure
Nessco Paper Cutlery Machine Catalogue
Want to Know More? Enquire Now
Download Brochure
Nessco Paper Cutlery Machine Catalogue